PLYWOOD
Plywood is made by laminating miscellaneous wood veneer and glue, and generally uses cross pressing between horizontal and rigid. The purpose is to enhance strength. Generally, a plate with a thickness of 12 millimeters or more requires 9 layers or more, and a plate with a thickness of 10 millimeters or more requires 5 layers or more. Plywood can be classified into four categories: weather resistant and moisture resistant plywood is classified as Class I, water resistant plywood is classified as Class II, moisture resistant plywood is classified as Class III, and non moisture resistant plywood is classified as Class IIIII. The prices of different categories vary greatly and should be selected according to different purposes.
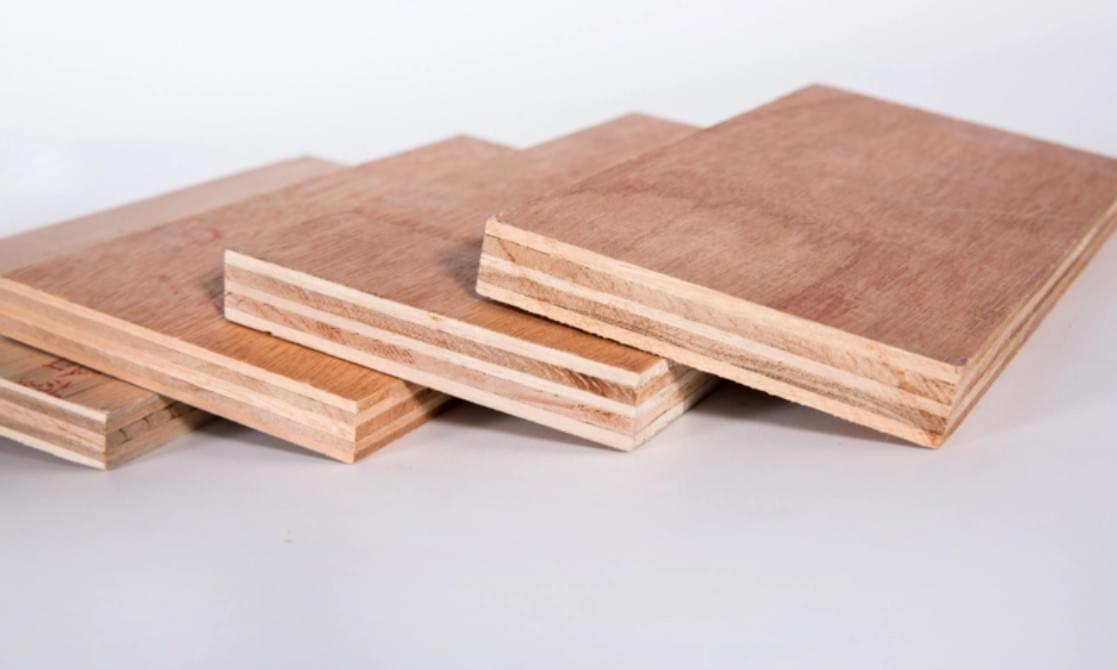
MDF
Fiberboard is made by hot pressing and laminating wood after fiber separation. It is divided into high density and medium density according to density. Medium density fiberboard is commonly used, with a specific gravity of about 0.8. Its advantages are smooth surface, easy to stick Boeing film, spray adhesive and stick cloth, not easy to absorb moisture and deform. Its disadvantages are that the effective drilling times are less than particle board, and the price is 5~10% higher than particle board.
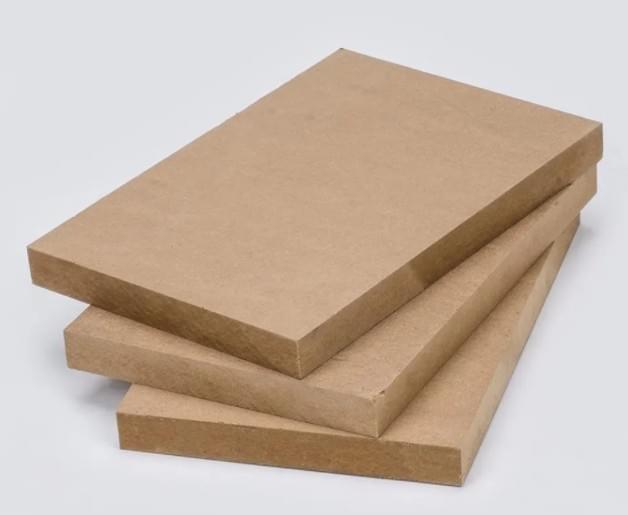
PARTICLE BOARD
A man-made board made from wood or other wood cellulose materials, with adhesive applied and then bonded under heat and pressure. Also known as particle board. Mainly used in the furniture and construction industry, as well as in the manufacturing of train and car carriages. Particle board is divided into three types according to product density: low density (0.25~0.45 g/cm3), medium density (0.55~0.70 g/cm3) and high density (0.75~1.3 g/cm3). Usually, 0.65~0.75 g/cm3 density particle board is produced. According to the slab structure, it is divided into single-layer, three-layer (including multi-layer), and gradient structure. According to water resistance, it is divided into indoor water resistance and outdoor water resistance. There are two types of particle arrangement in the slab: directional and random. In addition, there are particle board made of non wood materials such as cotton stalk, hemp stalk, bagasse, rice husk, and cement wood wool board, cement particle board made of inorganic adhesive materials. Particle board has many specifications, with the thickness ranging from 1.6 mm to 75 mm. The standard thickness is 19 mm, and the commonly used thickness is 13 mm, 16 mm and 19 mm.
As the basis for evaluating the quality of particle board and the main properties considered in use, the physical properties include density, moisture content, water absorption, thickness expansion, etc; In terms of mechanical properties, there are static bending strength, vertical plate tensile strength (internal bonding strength), nail holding force, elastic modulus, and rigid modulus; In terms of process properties, there are machinability, gluability, paint finishing, etc. For special purpose particle board, its electrical, acoustic, thermal, anti-corrosion, fire and flame retardant properties should be considered according to different uses. The production methods of particle board can be divided into flat pressing method, extrusion method and rolling method according to the different slab forming and hot pressing process equipment. The flat pressing method is intermittent production, while the extrusion and rolling methods are continuous production. In actual production, the flat pressing method is mainly used.
Particle board is a thin board made of wood chips, glue and additives. According to the pressing method, it can be divided into extruded particle board and flat pressed particle board. The main advantage of this type of board is its extremely cheap price. Its drawbacks are also obvious: extremely poor strength. It is generally not suitable for making larger or mechanical furniture.
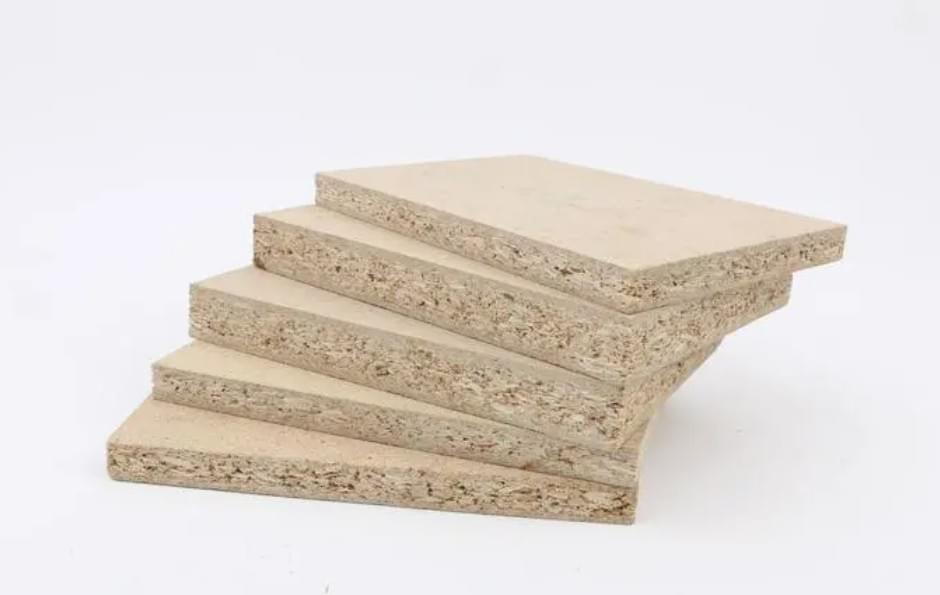